Manufacturing Readiness Levels (MRLs) and Technology Readiness Levels (TRLs) are two generally recognized methods to assess your technology and product for production readiness. These scales typically provide milestones and targeted accomplishments to determine “readiness” level with a 1 to 10 rating.
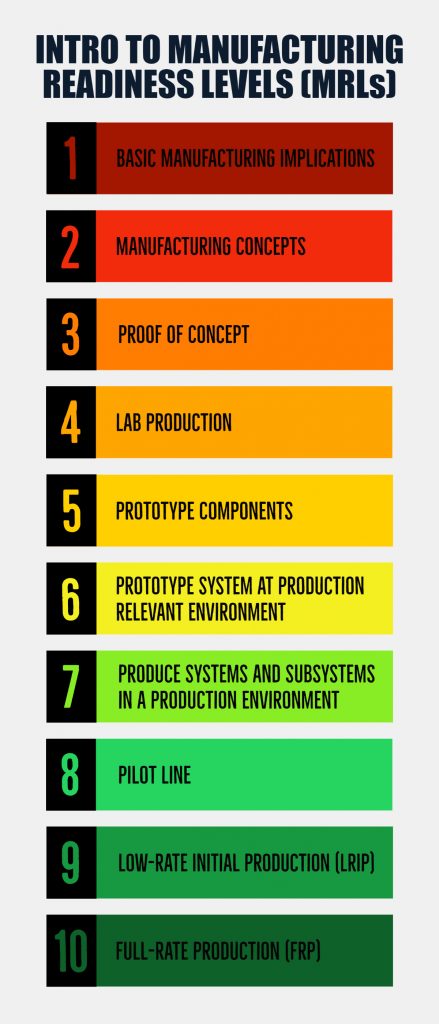
PEKO partners across many industries and corporation sizes, including defense, medical, and early-stage innovators use these guidelines. There are many variations of TRL and MRL scales, which all follow a very similar sequence of assessments.
What are Manufacturing Readiness Levels?
Manufacturing Readiness Levels (MRL) are a system used to measure the degree of readiness for manufacturing a product. The MRL system is an adaptation of the military’s Defense Readiness Condition (DRC) system.
The system can be applied to a variety of products, but in this article, we will focus on specialty machinery, equipment, and hardware products.
The MRL system consists of ten levels, each with its own set of criteria to measure the level of readiness. Those ten levels are:
Level 1: Basic Manufacturing Implications
Level 2: Manufacturing Concepts
Level 3: Proof of Concept
Level 4: Lab Production
Level 5: Prototype Components
Level 6: Prototype System at Production Relevant Environment
Level 7: Produce Systems and Subsystems in a Production Environment
Level 8: Pilot Line
Level 9: Low-Rate Initial Production
Level 10: Full-Rate Production
How do Manufacturing Readiness Levels Apply to Machinery Manufacturing?
Below, we describe how each of the ten manufacturing readiness levels relates to commercializing a new machinery or hardware system. Designers and new product teams can use these MRL levels as a guideline to assess a product’s manufacturing readiness and to identify the maturity level of their manufacturing program.
- Basic Manufacturing Implications: This first level of manufacturing readiness includes basic research and takes a quick look at the feasibility and manufacturability of the system at various levels. Manufacturability and materials are hot topics here. Here, the constraints of cost, availability, lead times, and tolerances are scrutinized, at least superficially.
- Manufacturing Concepts: At this point, you may only have a CAD model or rendering. Tolerances may or may not be defined, but they certainly aren’t complete and not all the data is available. You might be getting some manufacturing input from component parts vendors. For COTS items, you might have a general spec and are working with vendors to find the correct servos, drives, bearings, and other important items.
- Proof of Concept: Once you reach this MRL, you’ve ideally made preliminary choices for material, fabricated parts, and components, based mostly on your research and simulation data. You may have even made some crude models in your lab, but with very limited functionality. Now, at the proof-of-concept MRL, you must validate your manufacturing concepts, including determining manufacturing feasibility, identifying manufacturing processes, and initiating a reproducibility assessment.
- Lab Production: Lab production is your first build phase. Manufacturing technologies and processes are being finalized. Your bill of materials (BOM) is starting to take shape but is only populated with the basics. You’re beginning to understand the major cost drivers, design performance parameters, and manufacturability risks of the product. Other manufacturing criteria like floor space, tooling, and labor expertise are identified. This small-scale prototyping unit will be a technology demonstration unit, but not yet a true prototype.
- Prototype Components: At this point, you’ve ordered and received custom fabricated components and COTS items. This is low volume so the vendors you’re using might not be the same as the production vendors, but they are representative of the equipment and processes used. At this MRL, your manufacturing strategy is further refined, based on initial prototyping. Here, you’ll be able to identify manufacturing issues, like tolerances on parts or manufacturability of frame members and the entire welded structure. Tooling and inspection issues may also arise, and even Design for Manufacturing and Assembly (DFMA) concepts will be more apparent upon the manufacture of some components. Cost models will have more relevance as you’ve actually produced parts.
- Prototype System at Production Relevant Environment: With the preliminary design completed and the majority of manufacturing processes defined, it is time to build a ‘looks-like feels-like” version of your machine, also known as a prototype. By this point in the process, most critical parts and components have been designed, manufacturability assessment is close to complete, and costing targets and supply chain are all accounted for to a high degree, but significant engineering and/or design changes may still be needed in the system itself.
- Produce Systems and Subsystems in a Production Environment: At this level of manufacturing readiness, you’ll begin to finalize the detailed design of the system. Here, all processes and procedures are being contemplated by production suppliers and the internal environment. All tooling, supply chain, and cost modeling are nearing completion, quality targets and testing procedures are being established, and all material specifications have been approved and are available to meet the planned pilot line build schedule.
- Pilot Line: Once you’ve reached MRL 8, the detailed machine design is nearly complete, and low-rate initial production (LRIP) can begin. All improvements to manufacturability that were previously identified have been implemented on the system and any other issues have been resolved. At this point, the line and manufacturing operations are set up to accept production manufacturing.
- Low-Rate Initial Production: Low-rate initial production, or LRIP, is the second-to-last MRL level. Here’s the first shot at building machinery in the production environment. All processes, quality systems, vendors, tooling, and more are in place and the team is manufacturing units. At this point in time, manufacturing development has been completed and your technology has reached maturity. The rate of manufacture is less than the full rate, but at this phase, the team is making sure they can hit all their targets before going full throttle. The process of LRIP assures adequate manufacturing capability, creates a base production line, provides production articles for operational testing, and begins an orderly ramp-up to full-rate production. It is intended to result in adequate and efficient manufacturing capacity. Before making the FRP decision, a manufacturing readiness and technology readiness assessment should be conducted. This’ll ensure that no outstanding risks will affect the programs’ ability to deliver the FRP requirements.
- Full-Rate Production: Full-rate production, or FRP, is the highest level of production readiness on the MRL scale. FRP is essentially the end goal of the MRL process. At this point, design changes are complete, manufacturing processes are under control, lean production practices are in place, and there should be no significant manufacturing risks remaining. Ideally, all components, fabrications, and items are moving through the process at the desired rates. Once transitioned to FRP, engineering, performance, quality, and reliability requirements have all been met, and engineering and design changes are generally limited to quality and cost improvements to increase attributes like throughput.
These ten steps listed above do not have to be hard and fast rules, but more of a guideline and even a self-assessment method. Ultimately, the MRL framework will help guide the process of new product development, but also help to create internal or contract manufacturing infrastructure.
As products progress through the higher MRL stages — from pilot runs to low-rate and eventually full-rate production — the need for scalable, repeatable system integration becomes essential. As products progress through the higher MRL stages — from pilot runs to low-rate and eventually full-rate production — the need for scalable, repeatable system integration becomes essential. PEKO’s contract assembly services help OEMs bridge this gap by combining sheet metal, machined parts, subassemblies, and electrical systems into complete builds that meet production-level standards and support final product readiness.
Other Factors to Consider for MRL for Machines and Equipment
Building machinery and equipment for full-rate production is a windy road but it can follow this general MRL framework and process. Furthermore, there is a sequence of Technology Readiness Levels, or TRLs, that are usually overlaid with this process, which adds a new element of complexity.
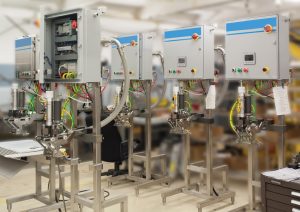
It is important to note that a particular TRL will often serve as a prerequisite to advance to the next MRL. Your technology will have reached the final level of TRL before it advances into the final two levels of MRL: low-rate initial production and full-rate production.
Understanding the MRL system is a good way to ensure your machines are being developed in the correct sequence and can even serve as a checklist against missing any important steps. Some institutions use milestones against certain steps of the process. As a contract manufacturer, we typically see our most successful programs coming to us at stages 5 to 6. This shows that the company is mature enough to start seeking outside and has the resources to answer technical questions from their contract manufacturer.
How mature is your manufacturing program? Do you know what your next step is?
We have created a comprehensive guide for OEMs and innovators that are bringing a new product to market. Whether you need design, development, or full-blow contract manufacturing, this self-assessment guide will help you reflect on the current state of your new product development program and what to do next.