Bringing Complex Systems Together
Precision integration for complex mechatronic and multi-disciplinary equipment.
PEKO provides custom system integration services for OEMs building advanced machinery and capital equipment. As a leading system integration company, we are your turnkey partner for projects that demand a seamless combination of mechanical, electrical, software, and controls — bringing complex subsystems together into fully functional, production-ready systems. When your project exceeds the limits of basic contract manufacturing, we provide the systems integration expertise that top OEMs rely on for high-performance, complex equipment builds.
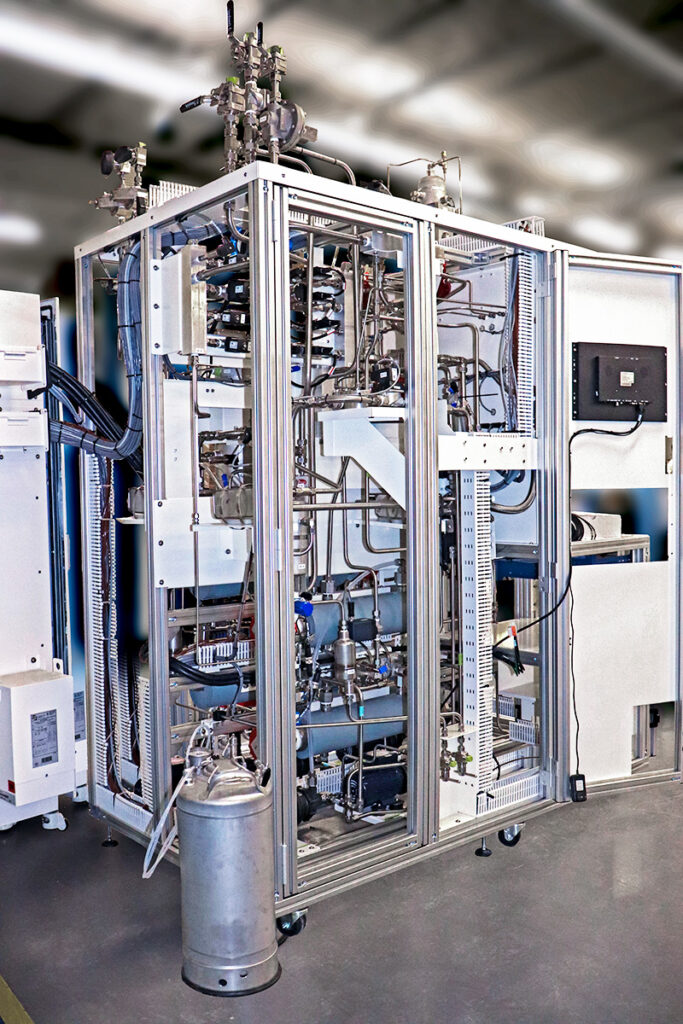
PEKO’s Role in Complex Systems Integration
At PEKO, system integration is at the core of what we do—especially for OEMs developing highly complex, capital-intensive machinery that demands precise coordination between multiple engineering disciplines. Our niche lies in building and integrating advanced systems where mechanical, electrical, software, and control technologies must operate flawlessly as one synchronized whole.
System integration at PEKO typically involves…
- Involve multi-level subassemblies across mechanical, electrical, and controls engineering disciplines
- Require functional testing, calibration, debugging, and compliance with industry standards
- Integrate motion systems, pneumatics, sensors, automation, and custom enclosures
- Demand rigorous documentation, configuration management, and product serialization
Our role begins wherever you need us—whether it’s early engineering consultation, prototyping and NPI builds, or final system integration and testing. Each program is treated as a long-term partnership, with a structured path from concept through production, ensuring your system performs reliably and is ready for deployment.
Why OEMs Trust PEKO for System Integration
- Cross-Disciplinary Expertise → Our teams have deep knowledge in mechanical design, electrical engineering, machine automation, controls integration, and software programming.
- Single-Source Manufacturing → We engineer, build, integrate, and test your entire system under one roof, with the majority of components machined, fabricated, and finished in-house.
- Engineering Collaboration → We offer Design for Manufacturing and Assembly (DFMA), custom fixture design, documentation reviews, debug support, and prototyping.
- Scalable Production Capacity → We have over 200,000 sq ft of dedicated assembly space, including ISO Class 6 (Class 1000) cleanrooms, prototype areas, and barcoded warehouses.
- Program Management → Our systems integration program is managed through stage gates, customer check-ins, and a team-based approach to scaling production.
- Product Lifecycle Support → From early-stage prototyping to full-scale production, we offer flexible involvement at any stage, tailoring our services to meet your exact needs.
- Customized Solutions → At PEKO, no two projects are alike. Every aspect of your integration — from specifications to tooling, testing protocols, and control strategies — is fully customizable.
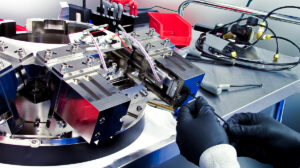
Our Proven Systems Integration Process
PEKO’s systems integration process follows a structured, bottom-up approach. Each individual module or subsystem is engineered, verified, and progressively assembled into fully integrated, higher-level systems through a structured series of phases.
-
Engineering & Planning
- Define product scope, performance requirements, and timelines
- Translate 2D/3D drawings, BOMs, and schematics into executable build plans
- Align on factory acceptance testing protocols and quality requirements
-
Part Sourcing & Fabrication
- In-house manufacture of precision machined and sheet metal fabricated parts
- Procure long-lead commercial off-the-shelf (COTS) components
- Conduct incoming inspection and pre-integration quality control checks
-
Subassembly Builds
- Mechanical and electromechanical assembly
- Sheet metal assemblies for brackets, skins and guards
- Conduct initial power-up and submodule testing
- Integrate software and firmware, as needed
-
Final System Integration
- Wire, route, and interconnect all components
- Program and configure control systems (PLC, HMI, motion control, etc.)
- Assemble into final enclosure or system frame
-
Functional Testing & FAT
- Simulate operating conditions with custom or customer-supplied test fixtures
- Execute full Factory Acceptance Testing (FAT) using documented procedures
- Generate traceable quality and compliance reports
-
Final Prep, Packaging & Delivery
- Complete labeling, serialization, and documentation
- Custom packaging and crating per customer requirements
- Secure delivery to final destination or customer site
Deep Expertise in System-Level Technologies
At PEKO, successful system integration goes far beyond installing hardware and running cables — it’s about orchestrating processes, technologies, and controls into a larger, smarter, and more efficient whole. Our integration experts possess deep, cross-functional knowledge of the hardware/software platforms and automation/control technologies essential for complex system integration, ensuring each disparate component works together with precision and repeatability.
Our areas of expertise include:
- Electromechanical Systems → Motors, gearboxes, actuators, and sensors
- Automation Controls → PLCs, HMIs, motion controllers, and drives
- Fluid & Pneumatics → Vacuum pumps, regulators, and flow systems
- Robotics → Cobots, multi-axis arms, pick-and-place systems
- Machine Vision → Cameras, lighting, image processing, and inspection tools
- Software Integration → SCADA, C#, Python, VB.Net, and customer APIs
- Instrumentation → Temperature, pressure, flow, and feedback sensors
- Safety Systems → Emergency stops, light curtains, interlocks, and relay logic
We seamlessly integrate third-party and customer-specified systems alongside our in-house fabricated components, ensuring all systems are powered, programmed, and verified for peak performance.
Comprehensive Engineering, Prototyping & Quality Management
PEKO delivers full support for your custom systems integration projects. As required, we can provide:
- On-site engineering support for DFM, DFA, FEA, and FMEA
- Prototyping and pilot production builds to refine designs
- Class 1000 cleanroom integration for sensitive applications
- Compliance with ISO 9001, ISO 13485, and AS9100 standards
- Full traceability, serialization, and regulatory documentation (UL, CE, FDA, ITAR/EAR)
- Intellectual Property (IP) protection and secure handling of proprietary information
Industries We Serve with Custom Systems Integration
Our custom systems integration capabilities extend across regulated and high-tech industries:
- Semiconductor & Clean Tech → High-spec tools for wafer processing and solar equipment
- Medical & Life Sciences → Diagnostic and therapeutic machines with mechanical + software integration
- Defense & Aerospace → Ruggedized, transportable, or specialty ground systems
- Industrial Equipment → Robotic cells, material handling systems, specialty automation platforms, and test rigs
Each industry has unique compliance, documentation, and environmental requirements — all of which PEKO is well-equipped to meet.
Let’s Build Complex Equipment Together
If you’re developing sophisticated machinery or capital equipment composed of numerous subsystems, and your team is stretched thin managing controls integration, automation, programming, and debug—PEKO is here to help. With decades of experience in industrial automation and control systems, we are your single-source partner for custom system integration—delivering engineered solutions that perform with precision and reliability. Whether you need build-to-print execution or full design/build support, our experts seamlessly plug into your workflow, allowing your team to stay focused on core innovation and IP.
Need a hands-on partner for your next system build? Start your project discussion today.