Nearly every sheet metal assembly contains sheet metal joints. From ducts to frames to skins, these sheet metal joints are extremely common but generally unknown to the common viewer. Sheet metal fabrication techniques create these special joints to enable the proper function of the higher-level assemblies in which they reside.
From the outside, you may only see a seam, bump, or nothing at all. Some common design choices for sheet metal joints are based on usage and seam characteristics. Things like material, pressure, thickness, and application come into the design consideration.
At PEKO, many of the sheet metal components we fabricate — using the joints and seams discussed below— become part of larger mechanical and electrical assemblies. Our contract assembly services bring together sheet metal, machined parts, wiring, and control systems to deliver complete, ready-to-use assemblies for OEMs across a range of industries.
Today we will look at 5 common types of fabricated sheet metal joints that are extremely common across the industry.
Lap Joints (Plain and Flush)
Forming a lap joint involves overlapping two edges in a specific manner.

Plain lap joint
A plain lap joint requires no fabrication and can be as simple as two edges offset simply by their thickness and some length along the edge.

Flush lap joint
In like manner, a flush lap joint involves offsetting one edge to slide under the other piece of material, with the face of each piece being on the same plane.
They can be joined in a wide range of methods like spot welding, solid welding, rivets, and soldering.
Standing Seam Joint
Another common type of sheet metal joint is the standing seam, which requires the forming of both edges.
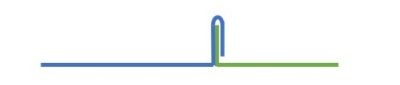
Standing seam joint
Firstly, bend the edge of the first piece at a 90-degree angle into a flange. Similarly, bend the edge of the second piece at a 90-degree angle, but with an additional hem formed over it. At this point, the hem will fit over the flange and can be joined with rivets or welds.
It is important to note that the standing seam protrusion must face the inside of the sheet metal fabrication assembly.
Standing seams are ideal for use in larger applications like plenums and skins.
Grooved Seam Joint
Another type of sheet metal joint is the grooved seam. As seen in the illustration, this joint is a curious combination of a flush lap and open hems.

Groove seam joint
Form the edges of two pieces into open hems that can subsequently be joined to create this type of joint. It is reminiscent of two hands locking fingers together.
Sometimes known as lock seams, they can speed up the assembly process by positioning themselves easily on one axis. Assemblers can quickly join the seams and a welder can clamp and weld into position with ease.
Corner Joints (Raw and Flange)
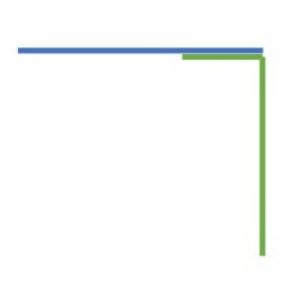
Raw and flange corner joint
The raw and flange corner joint is a type of sheet metal joint that closely resembles a plain lap joint and involves a flat stock piece joined to a 90-degree bend to form the corner.
To join the two pieces, overlap the flat piece (raw) across the corner bend (flange) and then join by spot weld, rivet, or solder. We suggest using tack or solid welding when joining heavy gauge materials.
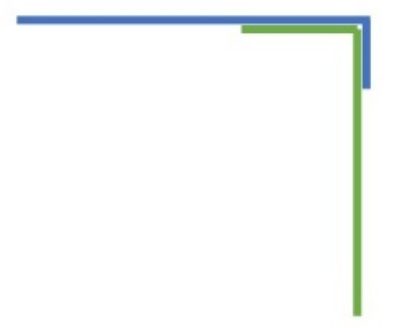
Flange and flange corner joint
Creating a flange joint involves forming a flange on each piece and then placing one on top of the other, with both types being formed in a similar fashion.
This sheet metal joint is good for flush outside corners and heavier gages.
Double Corner Seam Joint
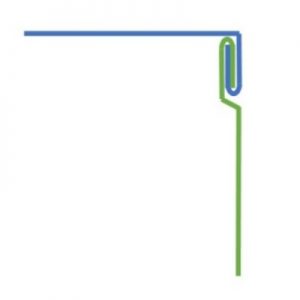
Double corner seam
Finally, the double corner seam is some kind of mix between a corner seam and a grooved seam.
Constructed with two open seams like a grooved seam, the double seam has a 90-degree angle to form a corner.
This joint is ideal for compound curves and may require special tooling to clasp it tightly.
Summing up, these 5 sheet metal joints are just a taste of the many dozens of joints that are available in sheet metal fabrication. It is important to keep in mind that to create full sheet metal fabrications and assemblies, you’ll need welding, joining, bending, and forming operations. For more information about sheet metal assemblies, download our 8-question checklist to ask yourself before selecting a sheet metal and welding fabricator for your project.
Share article: