Every entrepreneur in the startup category has some New Product Development (NPD) challenges to overcome. With ever-increasing technology options driven by smartphones, IoT, and 5G, software has become a major focus in terms of innovation. Great software developers pop up all across the country, especially in hot spots like Silicon Valley and Boston, but what about when it comes to hardware? From our perch, on the manufacturing side, we’re seeing incredible new startups with the most innovative software ideas that have one glaring problem: A lack of hardware new product development and equipment manufacturing knowledge.
The Importance of Hardware New Product Development for Innovative Startups
The fact is that these technology platforms are rooted in expert software programming and electronics, but the companies that are truly disruptive need a physical presence for the inputs and outputs. Smart lockers all over the world still consist of a metal locker, smart vending machines still need a piece of physical equipment to initiate the transaction, and Google’s Nest still needs a thermostat placed in the consumer’s home.
Startups with these unique ideas and capabilities may still have a major problem with developing their new product in the early stages, when it comes to the manufacturing of their technology’s hardware. Great software Startups understand this gap and look for companies that specialize in the hardware side of the equation, which is not as easy as it looks. PEKO has previously provided resources for finding a great contract manufacturer, but let’s dive into the three fundamental manufacturing pieces that must be completed in the hardware new product development phase before production can happen. Because face it, you and your investors are demanding an exponential growth curve, and it simply will not happen unless you can provide the hardware or equipment to deliver your software solution.
3 Fundamentals of Hardware New Product Development Success
Three fundamentals of NPD are actually the outputs of the initiative. These outputs will be the driving force when it comes to full-scale production manufacturing. These are typically happening concurrently with your prototype and alpha phases and are nearly complete by the time your pilot builds are finished. The three fundamentals are as follows:
1. CAD Models
What Are CAD Models?
CAD Models are two- or three-dimensional computer-aided design files that are the graphical and geometrical equivalents to your product. Companies like Solidworks, AutoCAD, and Creo all have platforms used in the mechanical engineering industry for decades. Most of the major CAD software companies offer free or reduced-priced packages for startups and students.
Why are CAD Models Important?
Startups usually have a mechanical engineer that draws and simulates the new product development hardware they are designing. When using CAD Models, each part of the assembly is documented and organized so changes are easily made. Revisions are stored, materials selected, and lifelike renditions outputted. Most CAD packages these days are programmed to simulate movement for functionality, stress analysis, output calculations, interface issues, and a whole host of other mechanical engineering acid tests. Visualizing your design and testing its functionality through CAD is one of the most important parts of this development process. This also sets up the manufacturing team for success since it provides a basic starting point for the manufacturing process.
2. Detail Drawings (Prints)
What are Detailed Drawings?
Detail drawings are the next level of manufacturing information. Manufacturing prints are two-dimensional files that carry all the manufacturing information for a specific part or assembly. These prints have important company-related information that includes company name, part number(s), and material types.
Why are Detailed Drawings Important?
Unlike a CAD model that gives a more natural visual representation, a detailed print shows a variety of standardized part views that the manufacturer uses to make the part. Sizes, locations, and tolerances for every feature are added to the drawing in a standardized fashion, most commonly ASME. Manufacturers not only use these prints to make the components and assemblies but during the part’s inspection as well because these detail prints are quite literally the blueprint that is subject to inspection to ensure the quality of the part is met. Detail drawings also include notes about finishing, special process information, tolerances, handling information, and other details about the part that must be communicated to the manufacturer. Usually, startup companies are not well versed in creating meaningful detail prints and require the help of a well-versed manufacturer with an established NPD process to tie up any loose ends.
3. Bill of Materials (BOM)
What is a Bill of Materials?
A bill of materials, also known as a BOM, is the comprehensive list of items that exist within the build of any assembly. Generally, BOMs include part numbers, revision numbers, suppliers, and quantities needed to manufacture the product.
Why are BOMs Important?
BOMs are vitally important in creating repeatable processes for manufacturing products but are often overlooked by startups focused on the research & development of their technology. It is absolutely critical to establish and control the BOM during the early phases of a hardware new product development, but in many cases, prototypes are built so fast and furiously that important changes to the build aren’t documented in the correct place. The bill of materials is essential for future builds because the organization and management of the parts needed on the products assembly drive the timeline of the entire build—if the parts that make up the assembly aren’t managed properly, how will the overall manufacturing of the hardware be managed? From the BOM, all parts of procurement flow, detail drawings are references and even sub-assemblies are organized coherently. As a contract manufacturer of hardware, we’ve seen countless startups ignore this critical document during this development stage.
For startups, it’s vital to your company that you stay educated on the best practices of these three fundamentals. Driving a manufacturable product that is repeatable is critical to having a successful new product introduction.
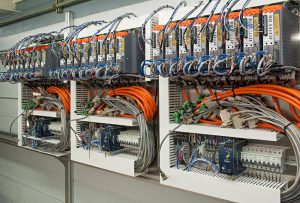
Be sure to either have your engineering group provide these fundamentals to a contract manufacturer or engage with a CM that can create them for you so you can reach the astronomical growth you promised your investors.
Have a great new technology that requires a hardware new product development and manufacturing partner to bring your idea to market? Request a quote and one of our new product development engineers will reach out.