If you’re a renewable energy company looking for precision and predictability for your product, CNC machining is a fabrication method that can give you the accuracy you want. But just what is CNC machining and what do you need to know about the process to decide if it’s right for your new product?
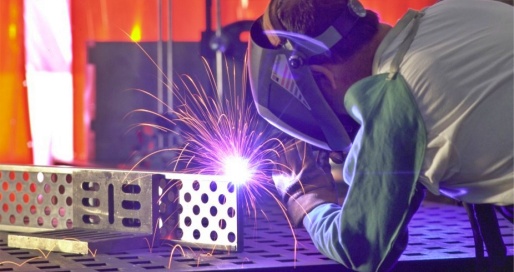
What is CNC Machining and How Does It Work?
As its name implies, at the heart of a CNC machine is a computer that automatically controls the machinery, whether it’s a mill, lathe, grinder, or other tools. With a CNC machine, a simple command is all that is needed to manufacture a variety of products. For this to happen, operators will pre-program instructions into software that will tell the CNC machine how to carry out the programmed tasks.
There are different types of software used in creating a part depending on what your production process requires. These include:
- CAD: The first step is to draw your part in a Computer-Aided Design (CAD) program. This software will produce either 2D or 3D designs as well as the technical documentation the CNC machine operator needs.
- CAM: After you have a CAD drawing, a Computer-Aided Manufacturing (CAM) program is used to take that drawing and convert it into what’s referred to as G-code. G-code tells the machine tool what to do, where and when. Think of it as a set of instructions.
- CAE: Often used within CAD, Computer-Aided Engineering (CAE) can simulate different conditions on the design of a product. This allows you to check how your model will respond when placed under different conditions.
These linked technologies will work to create your final part that meets your design requirements.
Understanding the Different Types of CNC Machines and Machining Processes
Depending on your renewable energy product’s CNC machining requirements, there are many different types of CNC machines available. Some of the most common ones that contract manufacturers of machinery and equipment used include:
- Mills: CNC mills are used to create shapes, holes, grooves, pockets, and more through the use of rotary cutting tools.
- Lathes: With a CNC lathe, a cutting tool shapes the part while the material block turns on a spindle. It’s used to make cylindrical parts.
- Plasma Cutters: With plasma cutters, a plasma torch is used to cut material. While they’re most commonly used on metal parts, they can be applied to other surfaces as well.
- Grinders: A CNC grinder uses a rotary wheel to grind or grate the materials into the desired shape.
- Drillers: CNC drillers drill holes or other shapes at a set diameter and length into a part set up beneath it.
- Routers: Similar to a CNC mill, a router is often a better choice for softer materials like wood or plastics and operates at higher rotational speeds to make its cuts.
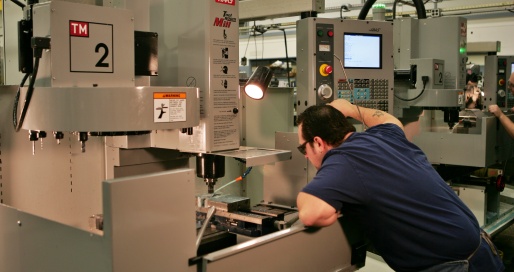
Also, some additional tools and components can be used within a CNC system for greater versatility, including turret punchers, wire-bending machines, and more.
Benefits of Using CNC Machining for Renewable Energy Product Fabrication
Ever since CNC machines were first available in the early 20th century, they have offered several distinct advantages. And these benefits still hold true for the renewable energy market today.
- Precision: If you have a part with tight tolerances, a high-precision CNC machine is an ideal choice to meet your specifications. That’s why they’re typically used to create parts that have a fine tolerance, like those used in the renewable energy industry.
- Greater Productivity: Since CNC machines are run by computers, they can operate even with workers aren’t present. This allows the machinery to run 24 hours a day if desired. The result? Fewer workers and increased production.
- Flexibility: With CNC machines, you’re not limited in your material selection. That’s because a CNC machine can make parts from a wide range of materials like metals, plastics, and even foam.
- Speed: With automation replacing human intervention, rapid CNC machining can do much more in less time, speeding the process between product design, prototyping, and manufacturing so you can go to market sooner.
- Less Waste: Most fabrication methods result in waste, which can increase your costs. Because of their precise nature, CNC machines make the most of every material to reduce the amount of waste.
While there are several pros with CNC machining, they may not be the right choice for everyone’s alternative energy project. Compared to other fabrication methods, the use of a CNC machine may cost more. Also, depending on the machine shop, they may not have the ability to handle your specific part such as a large-size parts.
How Do I Select the Right CNC Machining Partner for My Renewable Energy Product?
Fortunately, you have a lot of options when it comes to contract CNC machining shops for your renewable energy project. But that can also make it challenging to find the right partner for your needs.
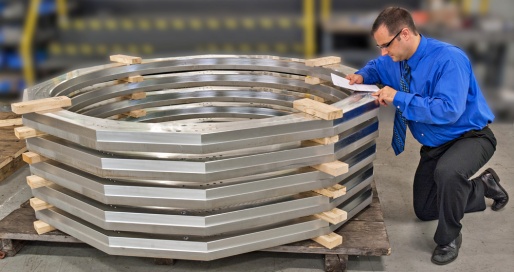
As you evaluate possible vendors, here are some things to look for:
- Tools & Equipment: Find out if the shop has the software and equipment to make your prototype or part. If you have specific requirements like for large parts CNC machining, make sure they have the capabilities to accommodate you. And confirm the equipment is up to date.
- Experience: The machinists at the shop you choose should be well-qualified and have extensive knowledge to handle the equipment. It’s a good idea to ask if you can see examples of previous work, especially of parts using the same material or for the same industry.
- Quality Measures: To avoid errors with your part, learn about the steps a shop takes to reduce risk. Ask about quality certifications like ISO 9001 and any strategies to aid in quality improvement like lean and six sigma.
- Customer Service: Your communication with a machine shop should be constant so find out how they work with customers. For example, will you have one contact person? Talking to previous customers can help you understand the level of service you can expect.
For renewable energy companies seeking precision and reliability in their products, CNC machining offers the accuracy needed for success.
By understanding the ins and outs of CNC machining and how it can benefit your new product, you can make informed decisions that align with your goals for quality and performance.
“With over 100 CNC machines and highly talented personnel, PEKO is the choice for hard-to-make parts,” said PEKO’s Vice President, Dan Brokaw.
If you’re ready to explore CNC machining further and find the ideal renewable energy contract manufacturer, download our checklist today. This resource will guide you through the process of selecting a partner who can bring your vision to life with top-notch precision and reliability.