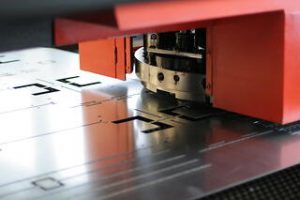
Across the USA, there are hundreds, even thousands of sheet metal fabrication shops. These shops support a huge number of OEM customers, defense contractors, and even hobbyists.
It is generally accepted that metal sheets of thickness under .250″ fall into the sheet metal category. Aluminum, stainless steel, copper, brass, galvanized, tin, and nickel are all available in their sheet metal form.
Here at PEKO, we have used our low-volume sheet metal fabrication division in unison with CNC machining and assembly. This gives a well-rounded approach to contract manufacturing and an ability to make frames, skins, and other components that roll into a large assembly. Other sheet metal specialists often opt to sell their services for simple component-level purchasing. Both are good approaches for the right customers.
The Difference Between High Volume & Low Volume Sheet Metal Fabrication Shops
Sheet metal fabrication shops themselves can be set up in a plethora of different ways to serve a multitude of different customers.
Some shops are set up for high volume production which means cycle time is more critical than setup time. These high-volume sheet metal shops are probably going to be full of automated sheet feeders, robotic loaders/unloaders, and other automated production and material handling equipment. Also, material handling becomes very important for moving a high volume of products around the shop.
Low volume sheet metal shops, however, are an entirely different animal. These shops will typically have more manual labor involved and are more concerned with lowering setup time so jobs can quickly be changed over. Furthermore, these shops usually have smart systems in place that can track all the different jobs and customers that are running on the same pieces of equipment.
Capabilities of Low Volume Sheet Metal Shops
There are many possible capabilities you’ll come across in a low-volume sheet metal fab shop. Below I’ll outline some of the more critical capabilities that you’d definitely expect to see to make the fabrication possible.
1. Forming and Bending
Forming and bending are critical to most fabrication products. When forming and bending, the metal sheets are bent into the desired features and angles with specialized machinery. Machines like panel benders and CNC press brakes are perfect for bending and forming operations.
A great low-volume sheet metal fabrication shop will have multi-axis press brakes to help lower both setup time and cycle time, like PEKO’s 8-axis brakes. The 8-axis brakes allow one to set up multiple forms on the same machine.
Having skilled programmers and operators make the job fast and easy to complete. These folks are highly knowledgeable when it comes to creative setups, force application, and process optimization.
2. Cutting
By choosing a manufacturer with a depth in cutting capabilities, customers can be assured that process optimization is being considered for their parts. Sheet metal cutting can be done with machinery like powered shears, CNC lasers and even CNC punches.
Each piece of machinery has pros and cons, and smart manufacturers set up their shop to optimize processes based on the parts coming through. A low-volume sheet metal fabrication shop might use the CNC laser for parts with intricate designs that must be cut or blanked with extreme precision and smooth edges. Conversely, a less sophisticated part can be quickly nibbled with a CNC turret punch at a high rate of speed and a lower cost.
3. Joining
Engineers have many methods for joining sheet metal such as swage nuts, welding, rivets, bonding, and clinching/folding. Any good shop should have a number of these methods at their disposal.
First, it will help to comply with the OEM’s original specification on the print. Second, it gives the fabricator an option to present to the OEM customer that might be a more functional or most cost-effective option.
A great low-volume sheet metal fabrication plant should certainly provide joining options like welding and riveting. At low volumes, it is very advantageous to have these options available for these types of products.
4. Powder Coating
In general terms, make sure your fabrication shop can provide cutting, forming, bending, and powder coating. These four capabilities above are certainly critical for a good low-volume sheet metal fabrication shop to have. There are dozens of other sheet metal operations, but these are certainly a critical baseline.
As mentioned, there are many different types of machinery and processes that can carry out these tasks, so it is important to make sure your product is optimized for the supplier.
For more information on sheet metal fabrication and how PEKO can help with your low volume, complex sheet metal jobs, contact us with your project requirements or download our guide of questions to ask when choosing a sheet metal fabricator for your project.
Share article: