When it comes to creating mechanical assemblies, metal parts manufacturing plays a crucial role in almost any industry. These components are vital to ensuring that machines and tools perform as intended, and their demand continues to increase because of their durability and strength.
But just how do you manufacture metal parts? In this blog post, we’ll cover three key considerations involved in the process of fabricating metal components, including material selection, fabrication methods, and part requirements.
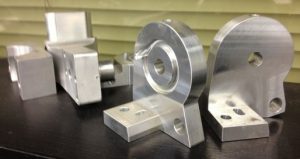
1. Selecting a Material Type
The first consideration in metal parts manufacturing is deciding on the material that will be used for the job. Various metals can be used to fabricate metal parts, and these metals can be categorized into two categories, hard and soft. Cost, weight, tensile strength, formability, machinability, and corrosion resistance are all important considerations when it comes to picking a metal for a part. Since different material types can affect a part’s performance, appearance, and cost, it’s essential to spend some time analyzing the characteristics of each option. By selecting the right material, manufacturers can ensure that the final product will meet the desired specifications and perform optimally.
Soft Metals:
Soft metals are prized for their malleability and lightweight properties. They are more comfortable to work with than hard metals and are ideal for creating parts with complex shapes and tight tolerances.
- Aluminum: Since aluminum in element form is soft, it’s not ideal for mechanical purposes. That’s why it’s typically blended with other elements such as copper, magnesium, and zinc, then heat-treated to improve its properties. Automotive and aircraft parts are commonly made from aluminum.
- Magnesium: Magnesium is a little more expensive than aluminum but offers some distinct advantages. Despite its lightweight, this material provides good strength and durability. It’s commonly alloyed with aluminum and zinc to make parts for household electronics like cell phone bodies and appliances.
- Brass: The highly versatile brass is an ideal choice when corrosion resistance is important. For example, many plumbing parts – like valves – are made of brass. It’s also incredibly strong and, depending on the ratio of brass used can fabricate everything from marine parts to coins.
- Copper: With its stringy structure, copper can be hard to machine. However, thanks to its electrical conductivity, copper is an extremely important metal for generating electricity and is often used in electrical wiring and tubing. Like other soft metals, it’s also commonly used as an element in many different metal alloys.
Hard Metals:
Hard metals are important functional materials when it comes to metal parts manufacturing, providing greater strength and durability. Like their softer counterparts, hard metals also each have their own unique properties and benefits.
- Steel: Steel is an iron alloy that contains about 1% carbon. Not only is steel a high-strength metal; but it also offers a lot of flexibility since it can be machined, stamped, roll-formed, welded, and more. This makes steel a universal material for metal parts.
- Stainless Steel: Stainless steel has the advantages of steel plus the added benefit of corrosion resistance thanks to an increased amount of chromium – 10% or more by weight. Stainless steel parts are commonly seen in marine applications and in chemical plants.
- Titanium: The biggest advantage of titanium is its strength. Yet it’s also lightweight, which accounts for its appeal and common use in aerospace, the medical industry, and the military. Because it’s also corrosion resistant, titanium is widely used in marine applications where metal parts will be exposed to water and rain.
2. Deciding Between Fabrication Methods
Once the material has been selected, the next step is to fabricate the metal part. Fabrication methods vary widely depending on the type of part that is being produced, and there are many factors to consider when choosing the right method for a given job. Various fabrication methods can produce different shapes and sizes to meet the desired specifications. Some common component fabrication methods include precision sheet metal fabrication, machining, joining, and welding. Understanding the pros and cons of each method is crucial in selecting which method will work best for their particular application.
Below are just a few examples. Since there are hundreds of methods to make metal parts, the requirements for each component will often dictate the best manufacturing process or combination of processes to use.
CNC Machining:
There are many types of CNC machines. Two of the most common are CNC mills, which are automated cutting machines, and CNC lathes which are used to turn round or bar parts. These machining technologies are commonly sought when manufacturing complex metal parts that require accuracy and detail since they are precise and repeatable. Since computer software controls a lot of the operation, costs can also be lower with CNC machines.
“Here at PEKO, our CNC Machine Shop and Sheet Metal Fabrication Shop provide the ability to manufacture the precision metal parts necessary in today’s high-tech machinery and equipment,” explained PEKO’s Manufacturing Engineering Manager, George Folwell.
Die Casting:
Die casting involves the use of a mold or die. It allows for the production of complex shapes with close tolerances. There’s little if any machining required and, since there aren’t separate parts fastened together, the piece can be stronger than parts made through other methods.
Injection Molding:
Metal injection molding is another fabrication method that requires little to no machining. With injection molding, a fine metal powder is mixed with a binder material and injected into a tool cavity. It can produce large quantities quickly and can also be cost-effective by eliminating manufacturing steps.
Sheet Metal Fabrication:
In sheet metal fabrication, thin sheets of metal are laser cut or bent to make custom parts. Less tooling time is required than with CNC machining yet sheet metal fabrication can also easily handle complex projects since the metal can be easily made into any shape.
Stamping:
Metal stamping uses both dies and stamping presses to fabricate sheet metal into the desired shape. Other metal forming techniques are also often involved like blanking and punching. Stamping is used in a variety of applications, especially those with three-dimensional designs or surface markings.
3. Understanding a Part’s Requirements
When it comes to manufacturing metal parts, some components are more difficult to produce than others. Simple parts can be made in a traditional machine shop, using standard equipment and tools. However, custom parts with specialized requirements may require more complex machinery and expertise. Besides specialized needs, custom parts might also require additional post-fabrication treatments such as surface finishing and heat treatment.
If a part has characteristics like difficult geometric tolerances, strict quality requirements, large overall dimensions, or tight process control, it’s best to work with a specialized metal fabricator who has experience in manufacturing complex components. Specialized metal fabricators, like PEKO, have the expertise and equipment to produce unique parts that meet the desired specifications, no matter how complex.
Metal parts manufacturing is a complex process that involves many different considerations. If you’re looking for a reliable and efficient way to manufacture metal parts, then you’ve come to the right place with PEKO. From selecting the best material for your part to the fabrication process itself, our team of experts takes the guesswork out of the complicated process of metal part fabrication—working closely with you every step along the way.
Whether it’s medical or aerospace grade components or just general components that require high-quality standards like complex geometric tolerances and strict quality requirements, PEKO is here to provide superior end results. Contact us today to get started!