Medical equipment manufacturers with new technology can benefit heavily in partnering with a full-service contract manufacturer. Established contract manufacturers have established supply chains, resources and capabilities needed to bring the medical equipment to market, while the Original Equipment Manufacturer can focus on the research and development end of their medical equipment.
Full-Service
One of the best benefits of having a turnkey production partner when you’re in the medical industry is the ability to leverage one company to manage the supply chain, manufacturing, assembly, and production of your technology. Rather than dealing with multiple fab-shops, and tracking down endless supply chains, consolidate all that work to one organization who will manage it for you.
When you work with a full-service organization, communication is open throughout the facilities. When outsourcing to a handful of small-sized machine shops, you rely on having to organize time frames from each shop—this can eat up a lot of time! When companies work with PEKO, they have one point of contact, their dedicated program manager who is the biggest internal advocate for our customers’ success. And since medical equipment requires quality checks throughout its manufacturing processes, by utilizing a contract manufacturer, companies can relocate their focus on more important aspects of their businesses.
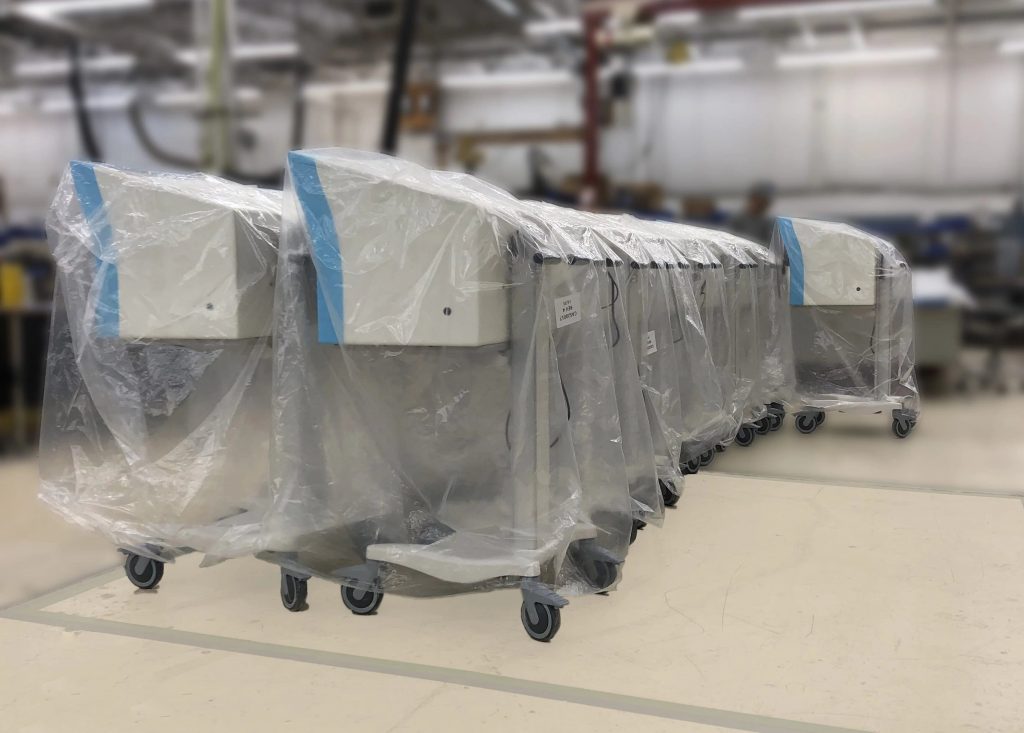
Quality Assurance & Quality Control
When it comes to manufacturing medical equipment, if parts or assemblies do not meet proper specifications, the end-user can find themselves in a life-or-death situation. Due to the severity of such consequences, PEKO’s quality management teams follow rigorous guidelines that OEMs and CMs alike must follow and abide by to ensure a technology’s success in the marketplace.
- The quality control team should be involved through various stages of component fabrication all the way through assembly and throughout the shipment stages. During our on-boarding stage, PEKO defines what criteria needs to be tested at each stage through manufacturing. For example, one of PEKO’s medical customers designed a large, complex MRI machine. This means that PEKO’s quality control team is responsible for quality checks on post manufacture components, any purchased parts, and all of the electrical and software units we have assembled. While this process may take more than 40 hours, it is essential to making sure the product is safe when it will be used in the medical field.
- The quality assurance team is involved with providing clear and traceable documentation with every part and process involved with manufacturing medical equipment. Documentation is an important aspect of manufacturing as a whole, but when it comes to devices for the medical industry everything needs to have clear traceability. The reason for this is simple: If anything were to go wrong with the device once it was in use, we would need to understand root cause.
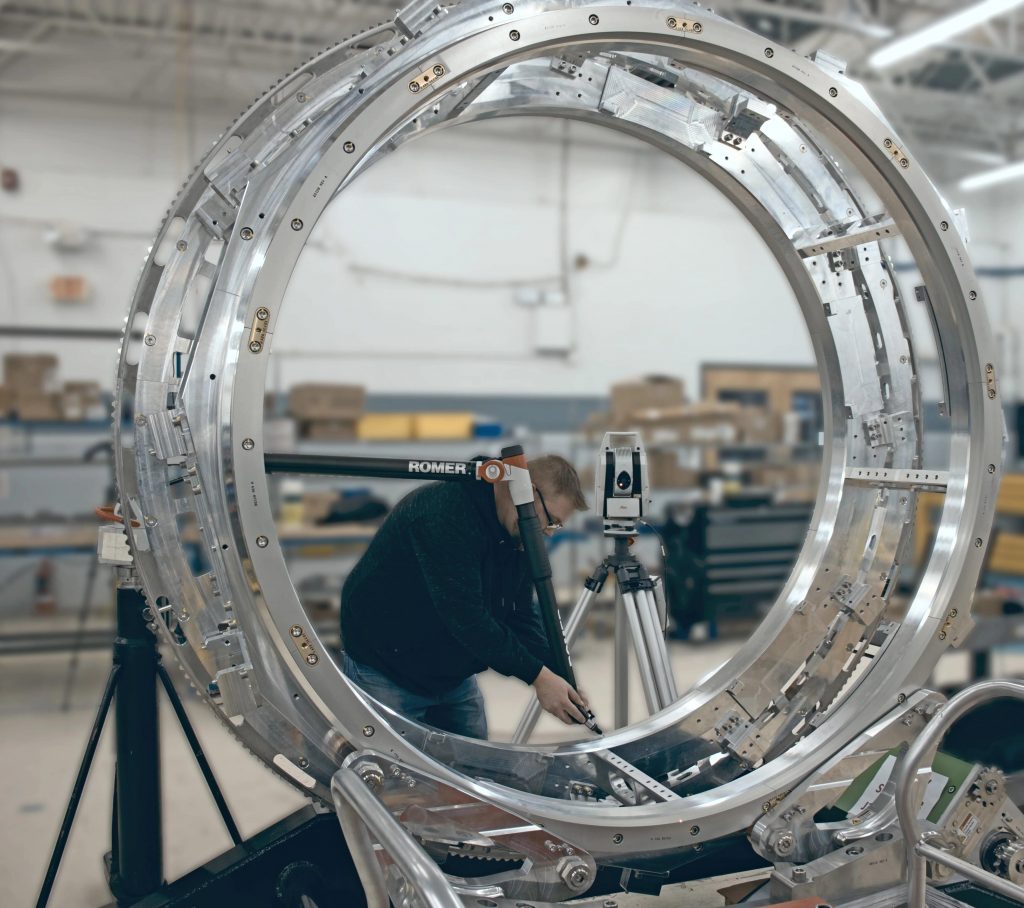
Packaging
The special care placed on manufacturing and assembling component parts for medical equipment needs to be followed through into the packaging. While importance is placed on making components, we need to know the sub-assemblies will make it to our customer, free of defect, as it could have serious implications on the end-user if anything happened during transit. This involves using proper packaging materials and crating to ensure safety of the product during shipment. In some instances, PEKO has made our own crating so our manufactured medical devices can make it to the end-user safely. In other instances, there may be customer requirements on shipping in regard to environmentally safe packaging materials in which we are happy to comply with.
PEKO has always been aware of the risks and enormous responsibility that comes with producing medical equipment for an original equipment manufacturer. All members of our PEKO team take great pride in the work we do because we know the effects that new medical technology and equipment have in our community. We understand that our personnel may have to rely on that same equipment to save their life or the life of a family member one day. That community dependence on safe, accurate and reliable medical equipment influences how we structure our quality management system so that we can meet strict regulatory compliance and provide satisfaction to our customer and ultimately the end user.
If you are interested in outsourcing your medical equipment to a contract manufacturer, check out our free checklist to help you get started!