When deciding to outsource new machinery or equipment builds, understanding the associated product development and manufacturing costs is critical. There are a lot of factors that go into the final machinery or equipment contract manufacturing cost.
3 Common Factors that Determine Machinery Contract Manufacturing Costs
In a previous blog post, we discussed the various methodologies and pricing models contract manufacturers use to estimate equipment manufacturing costs. In this blog post, we will take a more comprehensive look into contract manufacturing costs with a deep dive into non-recurring engineering (NRE), tooling, and minimum buy requirements.
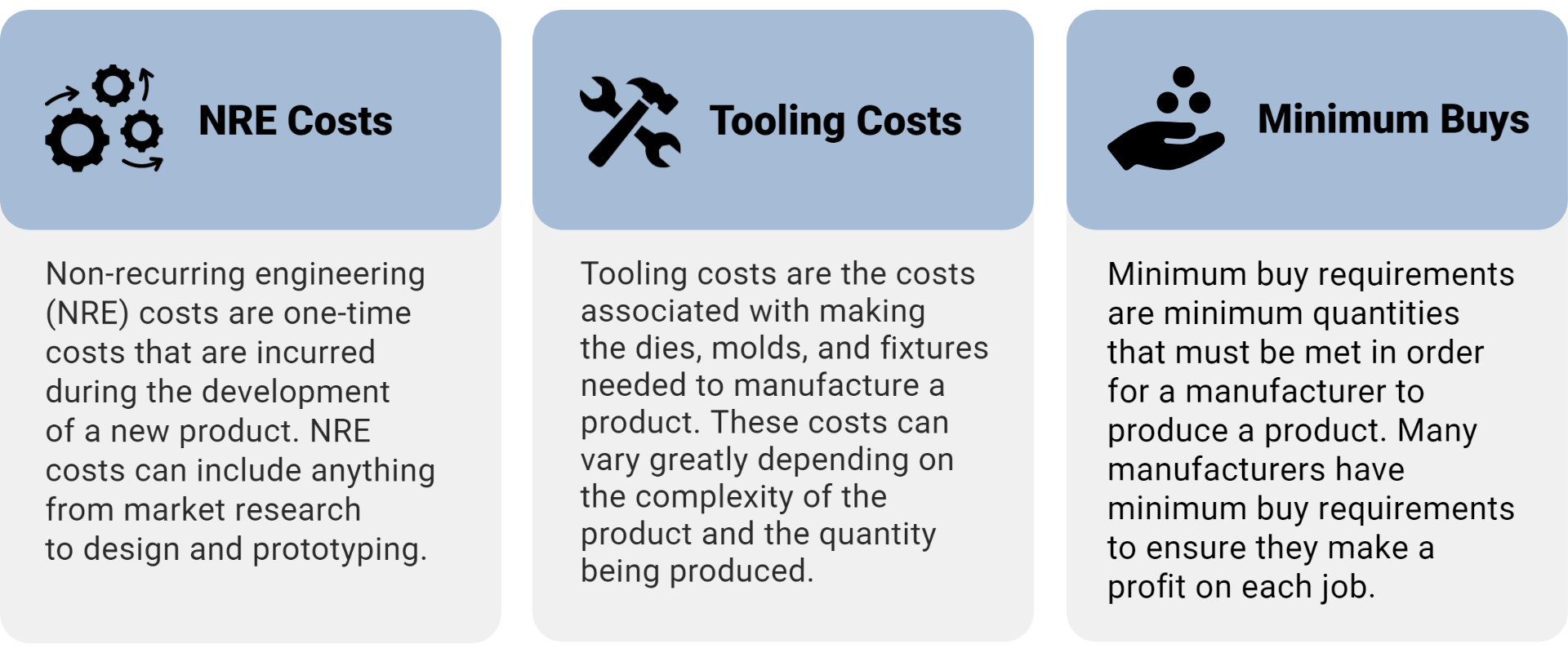
By the end of this post, you should have a better understanding of how these machinery contract manufacturing costs are calculated and what factors you need to consider when making decisions about product development and manufacturing.
1. Non-Recurring Engineering (NRE) Costs
Non-recurring engineering (NRE) costs are one-time costs that are incurred during the development of a new product. NRE costs can include anything from market research to design and prototyping. Once the product is in production, NRE costs are no longer incurred.
Typically, NRE costs make up a small percentage of the total manufacturing cost (usually less than 10%). For example, if the total project cost is $100,000 and the NRE cost is 10%, then the NRE cost would be $10,000.
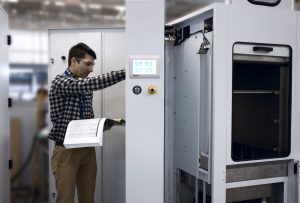
However, depending on the complexity of the product, NRE costs can be significant. For instance, developing a new aircraft engine might involve extensive testing, prototyping, and certification, which would result in high NRE costs.
Therefore, it is important to consider NRE costs when developing a new product. If the NRE costs are too high, it may not be possible to profitably produce the product. However, if the NRE costs are managed effectively, they can be a valuable investment in product development.
There can be hundreds of items that fall under the NRE cost umbrella, but here are a few common ones we see when providing design engineering assistance for machinery and equipment.
Special Programming:
One common NRE cost is special programming. This cost covers the programming that goes into part manufacturing. If your design requires custom or complex parts, the programming needed to manufacture those parts can add significant cost to your budget.
CAD Modeling:
Another common NRE cost is CAD modeling. This cost covers the time it takes for an engineer to create the CAD models. Creating CAD models is time-consuming and can be expensive, especially if you need to outsource the work.
Detailed Drawings:
In addition, once you have the CAD models, you’ll also need an engineer to create detailed drawings from them. This activity can also be costly and time-consuming.
Life Cycle Testing:
A fourth common NRE cost is life cycle testing. This cost covers the repeated testing time and fixturing done to determine the life cycle of a product. This type of testing can be costly, especially if it requires specialized equipment or fixturing.
Travel:
Finally, depending on the complexity of your product, the cost of sending engineering teams to visit plants or other sites related to your project would also fall under NRE costs.
2. Tooling Costs
Tooling costs are the costs associated with making the dies, molds, and fixtures needed to manufacture a product.
These costs can vary greatly depending on the complexity of the product and the quantity being produced. For example, simple injection molded plastic parts can be produced relatively cheaply, while more complex machined metal parts will be more expensive ranging into hundreds of thousands of dollars.
Tooling costs can be broken down into two categories: upfront tooling costs and ongoing tooling costs.
Upfront tooling costs are one-time expenses that are incurred when the initial set of tools is purchased. Upfront tooling costs can range from a few thousand dollars to millions of dollars, depending on the complexity of the product.
Ongoing tooling costs are recurring expenses that are incurred every time a new batch of products is produced, including things like maintenance and repairs for the tools as well as replacement parts that wear out over time. The amount of money spent on ongoing tooling costs will depend on the number of products that are produced as well as the frequency with which they are produced.
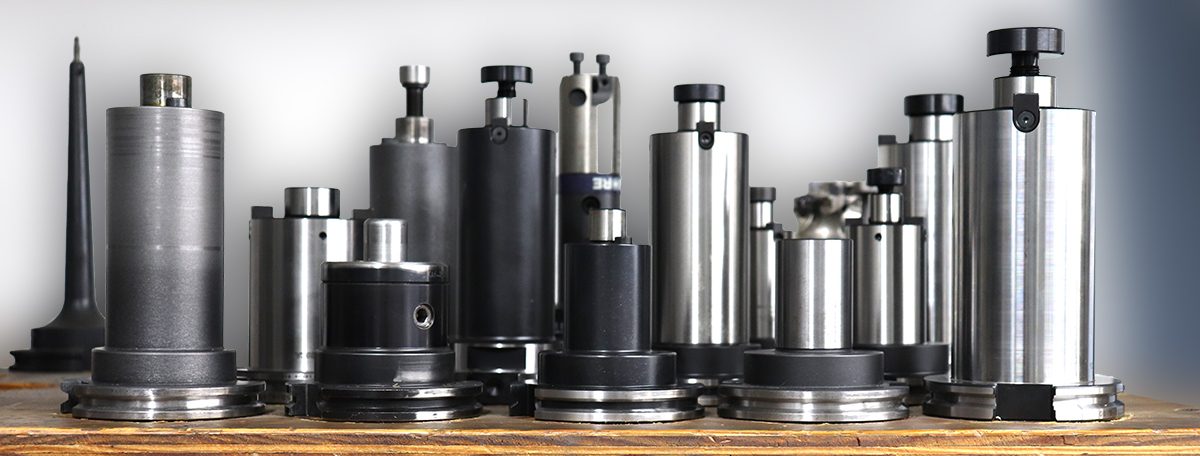
Tooling costs make up around 20-30% of the total manufacturing cost, so it is important to carefully consider tooling costs when designing a new product.
By understanding how tooling costs vary with different manufacturing processes, you can make informed decisions that can help reduce overall contract manufacturing costs. One way to save on tooling costs is to use standard or off-the-shelf components whenever possible.
3. Minimum Buy Requirements
Minimum buy requirements are minimum quantities that must be met for a contract manufacturer to produce a product. Many manufacturers have minimum buy requirements to ensure that they can make a profit on each job.
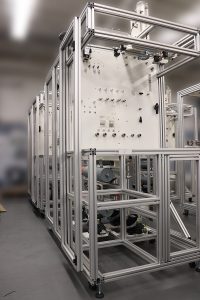
Minimum buy requirements can range from several hundred units to several thousand units depending on the manufacturer and the complexity of the product. If you do not need that many units right away, you may have to pay storage fees or other charges associated with holding onto inventory.
Minimum buys can be a burden for small businesses that don’t have the storage space or the cash flow to sustain a large inventory, but they can also be used as a negotiating tool to get better pricing from manufacturers.
Whether minimum buys are a good or bad thing depends on your individual circumstances.
When it comes to manufacturing, there are many different factors that contribute to the final cost of a product. By understanding these three cost factors, you can more accurately assess the true cost of bringing your product to market.
There are many other factors that will certainly affect your estimate, including product complexity, part size and quantity, materials, and processes, but by understanding the various contract manufacturing pricing models and these three cost factors, you can more accurately estimate the total contract manufacturing cost to bring a new product to market.
PEKO has extensive experience in manufacturing machinery and equipment for a variety of industries, so we can help you avoid surprises and stay on budget. Contact us today for an accurate price quote on your next machinery project.
If you’ve got some new machinery you need to be built, use our complimentary Guide to Choosing a Machinery and Equipment Contract Manufacturer to help you decide on the best pick for your business.
Share article: