Whether you’re on the hunt for a prototype, pilot, large, or legacy CNC machined parts, or considering entering the business yourself, it’s wise to have some knowledge on the manufacturing of these parts and the common theme you’ll notice in the best CNC machine shops. I’ve spoken to experts from all corners of our shop and combined, they share over 150 years of manufacturing experience to bring you these tips and tricks. From some of the answers I received, I could write an entire encyclopedia on the subject. For your sake of time, here are some of the hot button tips and tricks for manufacturing large CNC machined parts.
1. Temperature Control
When it comes to large parts CNC machining, everything becomes amplified, especially errors. Designs with features and positions with tight tolerances, held across long spans in a large CNC machine, are especially vulnerable to temperature variation. The variation comes from the coefficient of thermal expansion, CTE, for the base material, and even the components of the machinery. CTE is the rate at which material expands linearly for each degree of temperature change. For example:
— Aluminum has a CTE of 11.7 to 13.3 per degree (F) x10^-6
— Austenitic Stainless has a CTE of 11.7 to 13.3 per degree (F) x10^-6
Temperature control of the machinery and the base material that is machined is vitally important. In our experiences, we’ve seen rejectable variances between what was measured on the machine against what was measured in the Quality Control, QC, lab. We’ve had machine coolant systems chill the parts out of tolerance which caused parts to grow once they warmed up in our QC lab. With hard lessons like these, we, and now you can compensate with either machinery compensation or better coolant temperature controls on the machine. Even if you know this can happen, which we do, sometimes mistakes still happen the first time around.
2. Scrap or Prototype Pieces
Always have provisions for at least one scrap piece. The busier and more complicated parts, leave more chances for error. A 12ft long part with hundreds of holes, bosses, keyways, and other features, will be prone to errors at each step of the process. Errors in temperature control—discussed in the first section; programming; handling; machine capabilities; tooling selection; and others are prevalent in large parts CNC machining, regardless of the manufacturing company you partner with. If you’re a buyer within an organization, expect to pay more at the beginning for parts that are new to the market because the shop will need extra effort to execute your parts correctly. It is an investment, however, if you plan to take your parts to market with an increased rate of production later on, you’ll know a sound process was developed with the risk of future errors greatly reduced.
3. Offline Tool Verification
When it comes to machining large, expensive material blanks, it’s beneficial to either run the cutters on a blank piece of material and eat the cost, or in an area of the actual part that gets cut away anyways. This proves out the cutters, comps, and tapped hole sizes before running the part, eliminating the errors caused by dialing in tools on the sellable part. Take the time and extra work in this pre-processing step to set yourself up for success in the future.
4. Material Handling
More specifically, we’re talking about operator training here for overhead crane usage and safe lifting techniques. Very large are also quite fragile during the machine removal process. A wrong placed strap or lifting eye may cause many of the parts to buckle under their weight. Set up your facility with proper cranes and handling devices to improve safety and the chance of destroyed parts. Also, be sure to choose a great material handling company, as it is critical to your infrastructure. At PEKO, we enjoy working with GORBEL, and Bell & Howell.
5. Certifications
While this may be a bit off the cuff, it’s important to mention. Certifications don’t necessarily mean you will do a good job, but they are correlated with solid work and sound processes. Furthermore, industries such as Defense, Semiconductor, Communications, and Oil & Gas, are all ripe with large parts CNC machining requirements. All of which almost always demand at least an ISO9001 certification to do business. Combined with the fact that machining large parts is highly process-driven, the logical conclusion of earning a certification in an ISO standard is well worth the effort.
6. Inspection
Inspecting large parts CNC machining can be troublesome for many reasons. Special inspection machinery with a large bed is expensive. However, one way around these huge, pricey machines is to use portable coordinate measuring machines, such as a ROMER or FARO arm. These machines have their limitations, including precision measurements, but are easier to come by than a traditional gantry CMM.
Another trick is to implement laser inspection equipment to allow a “no-touch” inspection solution, coupled with other inspection techniques for ultra-precision measuring across large spans without a gantry CMM. For more information on this process, check out our review of this system here.
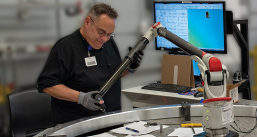
Find alternatives to the traditional CMM inspection method. Each time you measure a product on a CMM increases the number of times the product is moved for each required verification. This results in moving the part several times throughout a setup or run. Develop new inspection strategies or use portable measurement technology to significantly reduce machine downtime associated with verification activities.
Validate your new machines! Don’t use production parts to assess if a new machine performs as it is expected to. Instead, implement a robust validation strategy that allows for a confident assessment of the machine and if it performs as it’s intended to or not. Create test protocols to identify if the machine consistently meets the tolerances it was designed to, especially during reproduction runs.
5. Fixturing
Great fixtures produce great parts. With large parts especially, correct fixtures are vital to properly process parts to meet their required specs. Assign dedicated tooling/fixture personnel to help speed up the process. Fixtures for large parts CNC machining must contemplate the weight of the blank, the amount of stress added by the machining process, the location of holding devices, whether it can be re-used for inspection, the method of material handling, the thermal growth, the material movement during machining, and a host of other factors. A proper fixture is not cheap. Typically, large parts are custom-made and require multiple fixtures for their different operations. On the plus side, however, cleverly designed fixtures can offer some machinery flexibility to save time or cost. For instance, the ability to switch from a horizontal machine to a vertical one.
6. Programming
The programming for large parts is much different compared to their smaller counterparts. In our experience, it’s well-advised to train your programmers in performing offline programming, away from the machine. Incorporate a separate computer station with programming software like GIBBSCAM, to keep the focus and skillset strong. A great tip from our programming team is to break the program into submodules, when and if applicable. In other words, sections of code that can be verified. This helps organize and untangle some of the more complex programming demands necessary for large parts CNC machining.
As you can see, the topic of large parts CNC machining can easily expand from a blog post to an entire encyclopedia. Large parts CNC machining requires a delicate balance between art and science. Critical engineering and manufacturing input must be considered just as much as the machinery and shop conditions. As you delve deeper into this world, remember that PEKO stands out for its expertise and capabilities in precision CNC machining. To help you in evaluating and choosing a precision machine shop for your project, download our free checklist of eight critical questions to ask during your evaluation. If you’re curious about how PEKO can handle your CNC parts needs seamlessly, don’t hesitate to reach out and request a quote today.