In today’s highly specialized manufacturing world, companies demand precision, flexibility, and speed—especially when it comes to low volume high complexity equipment and machine assembly. Whether you’re working on prototypes, custom builds, or specialized systems, mastering the right assembly methods is key to delivering exceptional results.
At PEKO, we’ve built a reputation for delivering exceptional results in low-to-mid-volume machinery assembly. In this article, we’ll walk you through the top strategies that drive success in low volume manufacturing and offer solutions to common challenges faced along the way. Whether you’re an OEM or a product innovator, these insights will help you drive success from the shop floor to market launch.
Growing Need for Low Volume Manufacturing
Low volume manufacturing has become the go-to solution for companies that require agility, customization, and rapid product delivery without the massive investment of high-volume production.
This approach is ideal for:
- Pilot runs and prototypes
- Specialized equipment assembly
- Customized machine assembly
- Emerging technology production
But here’s the truth: success in low volume production hinges on having the right assembly methods—ones designed specifically for small-batch, high-value builds.
Assembly Methods That Drive Results in Low Volume Manufacturing Programs
1. Stay Organized Using 5S Methodology
Each low volume machine assembly project involves a unique combination of parts, tools, and processes—making organization not just helpful, but critical to success. One of the most effective systems for achieving this is the 5S methodology: Sort, Set in Order, Shine, Standardize, Sustain. This approach creates a clean, organized, and efficient workspace that reduces waste and streamlines workflow.
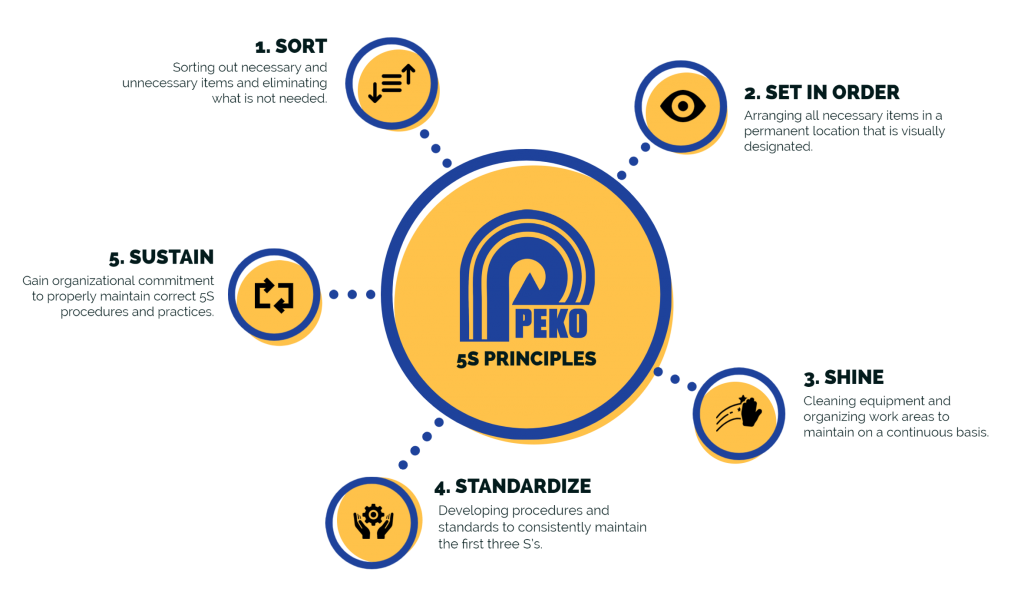
At its core, 5S emphasizes practices like clearly labeling equipment and parts, keeping the workspace clean, following standardized work instructions, and implementing well-defined processes that actively involve employees. When properly applied, 5S enables assembly teams to work with confidence and precision, cutting down on setup time and reducing the chance of misplaced or missing components.
Pro Tips for Setting Up a Successful 5S Program
- Optimize the flow of people and materials: Design the assembly area to minimize unnecessary movement and reduce time spent on each task. This not only cuts down on wasted motion but also ensures the process remains efficient, repeatable, and scalable.
- Track key performance metrics: Monitor labor hours, build rates, and recurring issues closely. By doing so, your operations team can quickly identify bottlenecks and implement solutions that improve both efficiency and product quality.
2. Use Time Tracking to Stay on Schedule
For machine assembly, where precision tasks like wiring, calibration, or system integration can vary widely between builds, effective time management is essential. Every hour matters when delivering small-batch, custom machinery on tight deadlines. To keep projects on track, it’s critical to compare actual hours worked against budgeted hours—this allows teams to spot bottlenecks early and take corrective action before delays or cost overruns occur. Accurate time tracking plays a central role in this process. Ensuring that employees are well-trained to log their time for each job pays big dividends in on-time delivery.
3. Prioritize Safety & Work Environment
Safety is always a priority in manufacturing, but it’s especially critical in low volume machine assembly, where teams often work on large, complex, or heavy components that require specialized handling. At PEKO, safety is deeply embedded in every assembly method we use. A robust safety culture delivers measurable success by protecting workers from injury and cultivating a positive work environment that provides employees with the assurance that we care. In short, a safe environment is a productive environment — and in small-batch machine builds, that translates directly to better quality and on-time delivery.
4. Continuously Improve Your Processes
Low volume manufacturing is rarely about doing the same thing over and over — it’s about refining and improving with every build. That’s why continuous improvement is at the heart of successful machine assembly.
By reviewing past performance and staying up to date on the latest manufacturing innovations, teams can refine their assembly methods to:
- Eliminate inefficiencies unnecessary steps
- Reduce waste (rejects, reworks, etc.)
- Improve tooling or fixturing
- Introduce better materials
- Implement automation, where appropriate
- Optimize quality checks at critical stages
Even small process improvements can lead to significant gains over time — reducing build times, improving reliability, and increasing customer satisfaction in subsequent projects.
5. Optimizing Assembly Area Layout
In machine assembly, the physical arrangement of people, parts, and equipment within the assembly area has a massive impact on efficiency.
Before scaling production, it’s critical to review the layout of your equipment assembly area, asking yourself questions like:
- Does the flow of people and material make sense?
- Are electricity, air, and water utilities accessible?
- Can you streamline steps by repositioning machines or tools?
PEKO invests significant time upfront in designing efficient assembly layouts that are tailored to each project’s specific needs. For complex machinery builds, we create dedicated assembly cells that house everything needed for the project, improving focus and reducing crossover between projects.
6. Use Dedicated CAD Workstations
Access to accurate CAD models, drawings, and manufacturing packages is critical in equipment assembly, where projects often involve intricate systems, tight tolerances, and evolving design requirements.
PEKO uses dedicated, secure CAD workstations for every major assembly program. This ensures that assembly teams always have access to:
- The latest design files and 3D models
- Up-to-date instructions and documentation
- Real-time engineering updates and change orders
With fast access to accurate technical data, teams can avoid miscommunication, reduce rework, and ensure every build meets exact specifications — critical factors when dealing with custom or highly engineered equipment.
Overcoming Common Challenges in Low Volume Machine & Equipment Assembly
Challenge #1: First-Time Builds & NPI Success
In low volume manufacturing, many projects involve first-time builds or prototype runs. These projects often have evolving designs, incomplete documentation, and unknown production variables, making it difficult to follow a predictable assembly path. Without a clear roadmap, the risk of errors, delays, and cost overruns increases significantly.
This is why PEKO has a dedicated New Product Introduction (NPI) team that specializes in managing first-time builds. It’s this department that is responsible for many important activities that lay the foundation for a project’s success once it hits full-scale production, like:
- Building rapport with our new customers
- Assessing designs for manufacturability
- Identifying cost-down opportunities
- Ensuring a seamless transition to assembly
Challenge #2: Employee Skills Development
Low volume machine and equipment assembly often require specialized skills — from interpreting complex blueprints and wiring diagrams to handling custom components and performing precision alignments. Many manufacturers struggle with having the right mix of talent on the floor, which can result in inconsistent quality and slower production.
To overcome this barrier, PEKO invests heavily in on-the-job training, cross-training programs, and outside courses for employees to build key skills like blueprint reading and manufacturing package interpretation. This commitment to workforce development ensures that every build is completed by a highly skilled, adaptable team
Challenge #3: Managing Complex BOMs
Machinery assembly projects often come with intricate Bills of Materials (BOMs) that include hundreds or even thousands of parts — from custom-machined components to off-the-shelf motors, sensors, and fasteners. Coordinating procurement, inventory, and logistics for such complex builds can overwhelm internal teams and threaten timelines.
This is one of the key benefits of working with a full-service contract manufacturer like PEKO. Our fully integrated supply chain management team handles every aspect of BOM management. By removing this burden from our customers, we enable them to focus solely on innovation and R&D, while we handle the complexity of sourcing, logistics, and part traceability.
Your Partner for Successful Machine Assembly
Low volume manufacturing is demanding — but with the right strategies, expertise, and systems in place, it becomes a powerful engine for innovation and customer success. At PEKO, we are committed to providing our customers with efficient and effective assembly techniques, helping them overcome challenges and deliver complex machines with confidence, precision, and speed.
Ready to optimize your low volume machine assembly process? Contact PEKO for a consultation and discover how our expert team and proven assembly methods can elevate your next project.