When searching for a manufacturing partner, many OEMs assume that any precision machine shop can handle assembly and system integration work. After all, if a shop can machine high-precision parts, shouldn’t it also be able to assemble them into finished products?
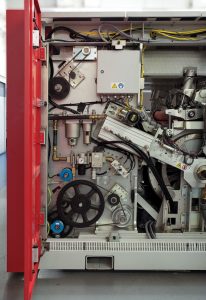
The short answer: not necessarily.
While precision machining is critical to the manufacturing process, the ability to perform full-scale assembly and system integration is an entirely different capability. Many machine shops simply aren’t equipped with the infrastructure, personnel, or processes required to build and test complete assemblies. Misunderstanding this distinction can lead to production delays, quality issues, and unexpected costs.
In this article, we’ll explore the key differences between a typical machine shop and a true contract assembly and integration partner like PEKO—and why it matters for your manufacturing programs.
The Gap Between Machining and Full Assembly and System Integration Capabilities
Many precision machine shops work hard to differentiate themselves in the market. They may offer value-added services like welding, painting, heat treating, or special materials handling. Some even offer basic assembly services for simple components.
But full-scale contract assembly and system integration is an entirely different ballgame. It involves more than bolting parts together — it requires assembling complex systems, integrating mechanical, electrical, and software components, and conducting rigorous functional testing to meet precise customer specifications.
What’s often misunderstood is the investment, expertise, and infrastructure required to deliver these services reliably. The truth is that assembly and integration work calls for dedicated facilities, specialized teams, robust program management, and significant capital investment. It’s not something that can be added to a shop’s capabilities overnight.
Key Differences Between Machine Shops and Contract Assembly and Integration Partners
Let’s explore the key differences between a typical machine shop and a true contract assembly and integration partner like PEKO.
1. Floor Space & Physical Setup
Traditional Machine Shops: Most shops are designed around CNC machines, tool rooms, and work-in-progress (WIP) staging areas. They may have limited or no space dedicated to large builds, subassembly cells, or dedicated integration areas. The shop’s layout and size play a crucial role in determining whether it can support complex assembly work.
Advanced Assembly Providers: State-of-the-art assembly and integration shops dedicate massive square footage to custom assembly cells.
For example, PEKO offers over 200,000 sq ft of assembly space with designated build bays, custom fixtures, and lift-assist equipment for low-to-medium volume capital equipment. This kind of infrastructure is essential for building complex machines and systems efficiently and safely.
2. Assembly Personnel & Training
Traditional Machine Shops: Traditional shops are primarily staffed with machinists. While these professionals excel at fabricating precision parts, they may only handle basic fixture assembly or prototype work. There’s typically a lack of dedicated assembly technicians or engineers with the expertise to handle complex builds.
Advanced Assembly Providers: Top-tier contract manufacturers employ full teams of assembly technicians, electricians, and assembly engineers. These specialists have the training and experience to assemble everything from motion-controlled subassemblies to fully integrated machines. Having the right team is critical, as assembly requires a blend of mechanical knowledge, electrical expertise, and problem-solving skills.
3. Program Management
Traditional Machine Shops: Operate on a job-shop model, focusing on short-run production, fast turnarounds, and minimal documentation or traceability. These shops typically lack the program management infrastructure needed for large, multi-phase assembly projects.
Advanced Assembly Providers: Structured to support long-term, complex programs, advanced assembly and system integration partners offer comprehensive program management services. This includes project managers, travelers, serial number tracking, change control, stage-gated delivery, and detailed documentation. Such capabilities are critical when managing high-stakes assembly projects with multiple moving parts.
4. Testing & Integration Tools
Traditional Machine Shops: Testing is often limited to part verification — confirming dimensions, tolerances, or surface finishes. There’s typically little or no capacity for electrical integration, functional testing, or system-level verification.
Advanced Assembly Providers: These companies perform full functional testing using custom test stands, software simulation, and customer-provided specifications. Testing may include verifying motion control, electrical continuity, software functionality, and system performance. Without this level of testing, OEMs risk receiving products that fail once deployed in the field.
5. Engineering & Technical Support
Traditional Machine Shops: Most shops can offer part tolerancing support and design-for-machining input, helping customers adjust part designs to improve manufacturability. However, they often lack the engineering expertise needed for system integration, control panel design, or electrical troubleshooting.
Advanced Assembly Providers: Assembly and integration specialists provide full engineering support, including assembly fixture design, control panel layout, wire routing, documentation, and interface feedback.
This additional layer of support helps optimize product performance and ensures smooth integration between mechanical, electrical, and software systems.
The Misconception of “Easy” Assembly
Many manufacturers assume that adding assembly to a machine shop is as simple as adding a few workbenches and hiring extra hands. In reality, building a high-level assembly operation takes years of careful planning, significant investment, and dedicated leadership. This includes:
- Investing in intelligent manufacturing software like ERP or MRP systems to manage the flow of thousands of components across the assembly line.
- Developing customized assembly work cells designed for specific product lines.
- Building a skilled team of technicians, engineers, and managers with experience in assembly, integration, and testing.
Even with the right tools and systems, success hinges on time, experience, and deep process knowledge — things that can’t be fast-tracked or bought off the shelf.
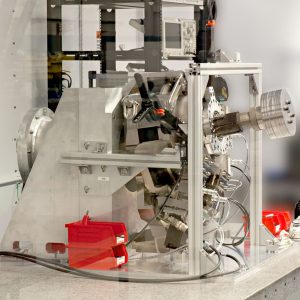
Why This Matters to OEMs
For OEMs, choosing the right manufacturing partner is critical. If your product requires more than just machined parts — such as system integration, testing, or functional verification — partnering with a true contract assembly provider is essential.
Here’s why:
- Reduced Vendor Count: Fewer handoffs mean fewer opportunities for error.
- Improved Consistency: End-to-end control leads to better quality and fewer surprises.
- Faster Time-to-Market: Coordinated fabrication and assembly under one roof accelerates delivery.
- Lower Risk: Experienced integration partners know how to navigate complex builds without derailing schedules or budgets.
How to Select the Right Assembly and System Integration Partner for Your Programs
When evaluating potential partners, OEMs should look beyond basic machining capabilities and ask:
- Does the company have dedicated assembly space and equipment?
- Do they employ trained assembly technicians, electricians, and engineers?
- Can they provide robust program management and documentation?
- Do they offer functional testing and system integration?
- Do they have experience with projects like yours?
A partner like PEKO offers all of these capabilities and more, acting as a true extension of your engineering and manufacturing teams.
Final Thoughts
Not all precision machine shops are equipped to perform assembly and system integration, and assuming they can leads to costly mistakes. OEMs that need integrated, tested, and ready-to-deploy products should partner with companies that have the right facilities, people, and processes in place.
By understanding the gap between machining and assembly — and knowing what to look for in a partner — OEMs can ensure they select a provider that delivers consistent, high-quality results from prototype to production.
Ready to Streamline Your Assembly Process? Download our free guide to learn how outsourcing assembly and system integration can help you cut costs, boost productivity, and accelerate your time to market.