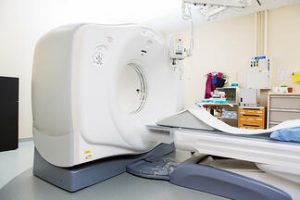
These days the medical and healthcare industries are booming but still susceptible to fluctuations. The medical industry is heavily impacted by an array of economic and policy factors. An aging global population, growth of emerging markets and health care M&A are just a few examples. Medical OEMs have to deal with the mitigation of these fluctuations in their manufacturing processes. Since the forecast can be unpredictable, OEMs must find ways to match their manufacturing with their demand, all without negatively impacting the bottom line. Ask any Manufacturing Manager, and that person will tell you that this is not an easy task.
One of the newest and most effective ways to deal with such uncertainty, is by utilizing a contract manufacturing partner with an ISO 13485 certification. In the past, assembly cells were setup throughout the manufacturing line, and items like analyzers, instrumentation and imaging devices were built right on the OEM floor. The challenge here was that demand shifts could cause an interruption in the process flow. These types of interruptions affect profitability in a big way. Resources cannot be predictably allocated, and delivery time can suffer. One buffer to help manage process interruptions was utilizing component manufacturing vendors such as CNC machine shops, sheet metal fabricators, cable harness assemblers, PCBA houses and plastic injection molders. By wisely using this supply base, OEMs can better optimize their lines to adjust for demand swings.
However, OEMs are starting to learn that by utilizing a contract manufacturer with more vertical integration, there are even more benefits to be reaped. A vertically integrated medical contract manufacturing company will be able to provide sub-assemblies and even finished product for the OEM customer. These types of CM’s usually will have a wide range of fabrication and assembly capabilities internally so they can provide the OEMs with more of the product in less time and typically for a cheaper price. If it is a sub-assembly, the OEM can use it in their internal line for final integration. This eliminates the need for more expensive and complex manufacturing lines. If the CM completes the finished product, the OEM typically only needs to manage expectations and utilize the CM as its own manufacturing extension.
One problem that Medical OEMs face when choosing a CM for their product is that becoming a medical contract manufacturer is not easy. There are stringent quality and traceability requirements that must be met and managed. CMs must also be familiar with the 501(k) submission process, as they may be part of it. Typically, the company is going to have to maintain an ISO 13485 quality cert for medical manufacturing. Not to mention extensive experience and knowledge of the QSR and CFR21. No matter which regulation has to be dealt with, preparation, organization, and discipline are keys to success. With a great Quality Management System, a CM can enable excellent record keeping, traceability, change control, and documentation control. This will help to mitigate regulatory roadblocks and ensure quality, delivery and performance are optimized.
PEKO Precision is exactly one of these Medical Contract Manufacturing partners. PEKO has experience with analyzers, medical imaging, and other equipment. For more information on how we can help build sub-assemblies or complete product, contact our team of experts today.