Industrial metal fabrication can be an art as much as a science. With today’s bending, forming, and cutting machinery technologies, it’s hard to believe the skill set that’s still involved in producing sheet metal fabricated parts, assemblies, and weldments.
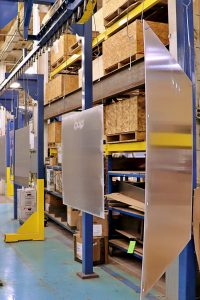
Any good contract manufacturer or sheet metal fabrication company will tell you that years of experience in metal fabrication are paramount.
The combination of seasoned sheet metal experts, new innovative technology, and the economic pressures of global competition have crafted a wealth of highly skilled sheet metal fabricators in the USA.
Those manufacturers that survived the overseas offshoring era have a rich knowledge of low-volume manufacturing techniques as well as high-volume production manufacturing technology prowess.
We’ve canvassed some of our own experts to give up some insider tips on sheet metal fabrication. Here are just a few of the secrets that I was able to pry from their metal-nicked hands.
Top Tips for Industrial Metal Fabrication
1. Specify A “Max” Inside Bend Radius
In industrial metal fabrication, how you specify bend radius is important. When we “flatten out” a part in CAD in programming, one must adjust for bend allowance, by adding material to each bend to allow for the shrinkage of material during forming. Not all materials shrink the same, and the amount of material added is based on the tooling radius.
Most sheet metal fabricators prefer that you design with a “Max” inside radius. Specifying a “Max” allows greater latitude, and sometimes allows us the ability to save parts that are on the edge of tolerance. That allows programming to vary the bend allowance to fit the tooling that will yield the best performance.
For example, if you specify a max bend radius of .060, the fabricator can choose a .008, .032, or .060 sized tool to get the best results.
2. Use Bump Forming for Bending Curves
Bump forming is a process by which a part is formed with very small incremental angles. This industrial metal fabrication process is performed on either a Panel Bender or Brake Press.
Bump forming requires more “hits” per part but allows us to make parts with large radii using standard tooling. The larger the radius, the more susceptible it is to variation in material thickness, or tensile strength, because of the number of hits required. We often create profile gages to make sure we stay on track.
Marketing loves a sleek radius, but there’s a cost. The part on the left in the image below was not the original design.
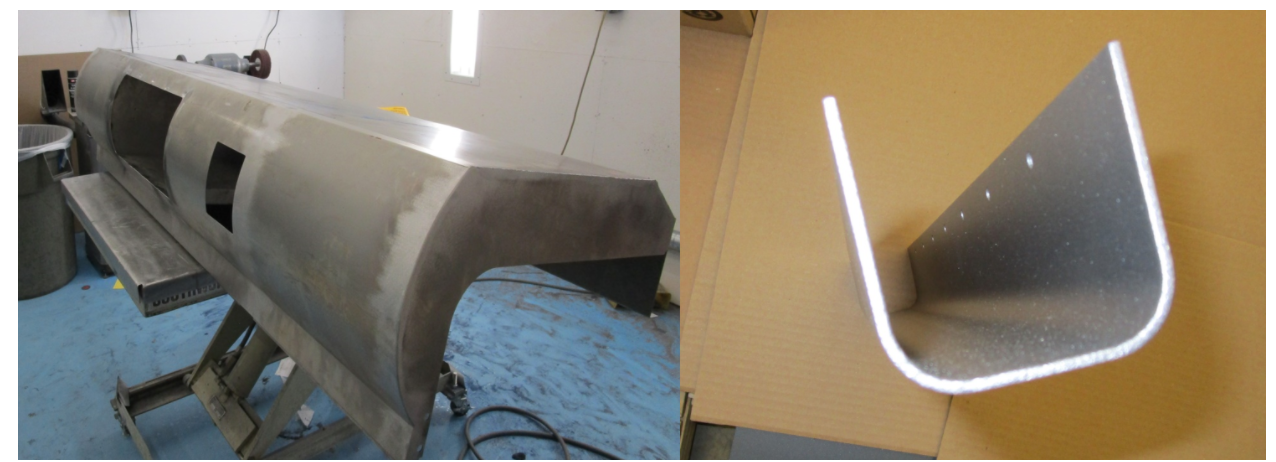
3. Utilize Cleco Fasteners for Temporary Fastening
Cleco Fasteners, often known as Clecos or Clekos, are temporary retractable rivets to hold surfaces together for welding. These fasteners require additional holes in the mating parts for locating that can be filled with a weld after use. Holes must be pre-drilled into the base material before they can be installed.
Clecos are great for use in panels or any other area where speed and repeatability are factors. They come in many standard shapes and sizes, are readily available, and can be installed with one hand.
4. Use Slot and Tab for Self-Locating Mating Parts
Use of slot and tab construction for self-locating mating parts in the middle of a part or notch and tab at welded corners to help self-locate.
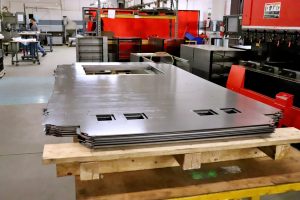
Using slot and tab techniques will speed up assembly time and drastically improve repeatability, especially at production volumes. Furthermore, they help to restrain adjacent surfaces against weld shrinkage.
Typically, these features are not designed directly into the prints by the design engineer. The fabricator and engineer will have to collaborate to ensure this is acceptable to the print and determine whether a note must be added to the prints to manufacture this way. In our experience as an industrial metal fabrication provider, the answer is usually yes.
Bonus: Quick Tips for Welding Fabrication
- Weld in sections on long seams, alternating back and forth along the seam to reduce distortion.
- When staging parts, allow for shrinkage when possible. For example, if there is a 90-degree angle, stage parts slightly open and utilize angularity tolerance to allow for shrinkage when corner seams are welded.
- When possible, utilize tack welds to reduce part movement prior to completing the weld.
- When welding an aluminum part, the cleanliness of the material and filler rod will have a significant impact on the quality of welds, especially during any testing requirements.
- Quality tooling and consumables (i.e., gas, filler rod, equipment, etc.) aid in producing quality weldments.
- Tab and slot location features can assist in self-locating component parts as well as squaring a corner seam.
- Purging argon through (inside) a stainless welded assembly can reduce inside weld discolor, impurities at the welded seam.
The experience that comes from years of welding, bending, forming is getting harder and harder to replace, and after speaking with the folks in our sheet metal fabrication department, it’s easy to see why industrial metal fabrication companies need to cherish their in-house fabrication experts.
It’s important that articles like this exist to help keep the experience flowing around the industry, but even more important is for good people like our readers to take this knowledge, use it for your own fabrications and weldments, and expand your own knowledge base.
Whether you’re working at a high-end contract manufacturing operation like PEKO, or a 5-person metal fabrication company, take some of these tips and apply them to your processes today.
Are you looking for an industrial metal fabrication provider for your product? Download our guide for an eight-pack of critical questions to ask when selecting a sheet metal and welding fabricator.