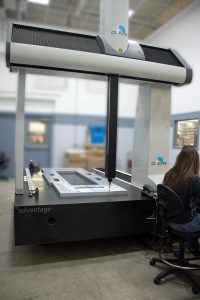
Discrepant products can not only affect the relationship a contract manufacturer has with their customer, but can also turn to be a life-or-death situation depending on what industry the product will be used in. If the contract manufacturer builds machinery and equipment for the heavily regulated defense and medical industries, then there are extra processes that are in place.
Quality Plans
In order for a program to be successful, there must be a robust quality assurance team to enforce that the quality plans are adhered to during the duration of the manufacturing company’s project. Quality plans have many purposes in a manufacturing environment.
First and foremost, a quality plan ensures that conformance is based on the customer’s requirements. If the customer is in a specific industry, such as the defense and medical industries, then there are extra standards that must be outlined in the quality plan since compliance to a product’s specifications can put the end user in life-or-death situations, if the product has not been manufactured correctly.
A great CM will include a customer’s goals and objectives in the quality plan, along with processes, procedures, and the distribution of responsibilities. This is so the manufacturer can work with the customer’s end goal in mind. At PEKO, our superior quality system is integral to customer satisfaction and the mutual success of PEKO and our partners.
Quality Control
Having a robust quality control plan in place identifies and, if applicable, corrects any nonconforming material or finished product before shipments are made to the customer or end-user. When nonconforming products are identified, it is the responsibility of the Quality Control Team to fix the defected material if suitable, and also identify how and where the defect took place. When robust quality control processes are in place, then corrective measures will take place to make sure the defect does not happen again.
A robust quality system that includes quality assurance and control teams are essential for high-quality and well-defined end products that are produced within a contract manufacturing facility. All nonconforming material should be assessed through the Quality Control Team while historical records should be kept for full transparency.
If you’re interested in outsourcing your manufacturing and would like more information on how PEKO can help drive your success in the marketplace, request a quote today!