Share article:
Design for Manufacturability (DFM) is the younger sibling to Design for Manufacturing and Assembly (DFMA) and cousins to Value Engineering, though sometimes the words are used interchangeably. No sense in splitting hairs, but Strictly speaking, DFM is concerned with the production of parts and low-level assemblies that will be later integrated at final assembly. As they say, there are many ways to the top of the mountain, and the same is true in DFM. It takes manufacturing process knowledge, forecast expectations, and a little bit of creativity to pull off some very effective DFM strategies. Since we’ve had hundreds of successful DFM projects under our roof, I’ll share with you some simple and effective DFM tweaks that you can implement sooner today, direct from a Contract Manufacturing company right here in the USA. Consider this your Design for Manufacturability 101.
Combining Multiple Parts
Combining multiple parts into one part is something of DFM 101. Especially during the design and prototype phases, the engineer adds parts and features because the goal is simply to prove functionality and get some semblance of the final product. This is a normal and effective part of the process. The unfortunate part is that occasionally the new product development team misses the opportunity to revisit the design to understand if any parts can be combined or eliminated once they’ve proven functionality. In many cases, features like bosses, faces, plates, adapters, and others are created at the part level. A great way to combine these is to design them into a single machined or sheet metal fabricated plate. Now you’ve eliminated parts manufacturing, supply chain management and even hardware. In most cases, assembly time will be reduced too. Your mileage may vary but this usually comes at the small expense of some engineering time and creativity, combined with some manufactured parts quote requests to ensure the new design is viable and cost-effective. Below you’ll see a sub-assembly where the original design included (64) CNC machined pieces which we reduced to (2) double-wall sheet metal fabrications and (8) CNC machined pieces
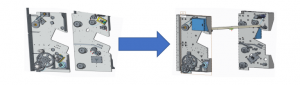
COTS Items
Commercial off-the-shelf items are great because they are typically inexpensive compared to their custom counter parts, readily available and oftentimes the CAD models can be obtained so you can easily import them into your CAD design. Strangely, in the heat of the moment, we see that engineers wil design more custom parts than necessary to meet their design requirements. I can’t count how many times we’ve seen machinery or equipment prints come across our desk chock full of custom shafts, springs, shims, spacers, tubes, bolts, and other items. For product managers and other product design personnel, it’s very valuable to educate your team on ways to substitute custom parts for off-the-shelf items. These days, standard industrial distributors like McMaster Carr and Grainger have a wide variety. This may seem like an obvious and simple design change, but it is often overlooked after the fact and deserves a second look into existing or early stage designs.
Convert Weldments to Boltments
In most machinery and equipment, there is some frame structure that is the backbone of the design. Although this tweak is a little trickier and your team will have to be well versed in structural analysis and fabrication, I highly recommend looking into it. Frames and weldments can be very expensive to fabricate. Most Contract Manufacturers will tell you this. There is a lot of labor that goes into setting up weld fixtures and the labor associated with welding can be very costly. By converting to boltments, you can design the critical alignment features into the lower-level components. Slots and tabs, bosses and other alignment features let a lower-level assembler line up the parts, then quickly bolt the pieces together. Furthermore, the lower level components may even be good candidates for simple machined parts or even sheet metal fabricated parts. Size, geometry, datums, hole location and tolerances all play a big factor in this type of tweak, but with a little creativity, you can save a ton of money by optimizing your boltments. Pictured here, this weldment was converted to a boltment to improve the consistency and quality, eliminating a large number of operations, and resulting in a reduced unit cost as volumes increased significantly.
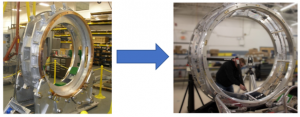
Tolerances
Copying design block tolerances from one part to the next is common and efficient, we all do it. But the fact is that the contract manufacturer is bound to these tolerances and other tolerances on the print as part of the quotation and manufacturing processes. Typical three-place tolerance is +/- .005”, but is it always necessary? We highly recommend that you go back to your designs and see if your tolerance callouts are all necessary. Make sure that non-critical features are toleranced as loosely as possible. Every single day we see component prints come our way with tolerances that are absolutely unnecessary so we have to quote them using very expensive machinery. The manufacturer doesn’t always have time to question the design tolerances to the engineering team (if the engineer is even available) so the product and design team should comb through their print tolerances to make sure that you haven’t over-toleranced your parts, causing expensive manufacturing techniques to be used.
Have a New Product Introduction project sitting on your desk? Take our contract manufacturing readiness self-assessment guide by filling out and submitting the form below!
Share article: